你是否也曾遇到这样的情况:一个看似完美的铸件,打磨后却发现表面坑坑洼洼,或者装配时才发现尺寸偏差、内部气孔?铸件看起来像是按图纸做的,却总是“差那么一点点”——力学性能不达标、外观瑕疵、甚至在客户手中提前失效。
金属铸造过程本身就充满了不确定性——高温、熔融金属、高压充型,每一个环节都可能成为缺陷的温床。从看得见的表面凹陷、飞边,到肉眼难辨的气孔、缩孔,铸造缺陷就像“潜伏的敌人”,稍有疏忽,就可能影响最终产品的质量和可靠性。
掌握这些缺陷的类型、成因与对策,正是每一位制造工程师、质控人员与铸造专家的基本功。本文章将带你系统梳理压铸过程中常见的各种缺陷,深入解析它们的成因机制,并提供实际可行的解决方案——帮助你把“问题”变成“可控”。
什么是铸造缺陷?

简单来说,铸造缺陷就是那些让零件无法达到质量标准的“瑕疵”或“不对劲的地方”。这些问题可能来自材料本身的质量不好,也可能是设备出故障了,或者是工艺流程设计得不够合理。
特别是在压铸过程中,尽管有些小瑕疵我们可以接受,但一旦铸件表面有缺陷,就可能会降低强度、影响外观,甚至无法正常使用。所以,识别并解决这些缺陷,是每个制造人员必须面对的挑战。
铸造缺陷种类繁多,但通常可以分为以下四大类:
接下来,我们就一起深入看看这些不同类型的铸造缺陷是怎么发生的,又该如何处理它们,避免它们“偷偷”破坏你的产品质量。
冶金缺陷
铸造看似只是把金属倒进模具,冷却后成型,实则远比想象中复杂。尤其是“冶金缺陷”,它们就像藏在金属内部的小麻烦,如果不加控制,不仅会影响外观,更可能让零件强度不足、提前“罢工”。
这类缺陷主要源于金属本身的行为,常见的有孔隙、缩孔和翘曲。
1. 孔隙缺陷:看不见的“空气洞”
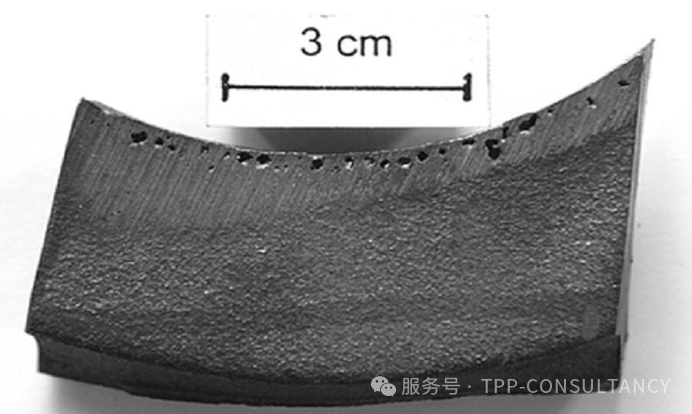
你可能没想到,金属里竟然也能藏气泡!这就是“孔隙缺陷”的本质。它是铸造中最常见的问题之一,也是最难察觉的“隐形杀手”。
当金属被高压注入模具时,如果流程不稳定或空气没来得及排出,就会有气体被困在里面。
等金属冷却了,这些气体形成小洞,分三种情况:
这些孔看起来像黄色或白色的小泡泡,有时在加工后才被发现。它们不仅影响美观,还会削弱金属强度。
它是怎么来的?
金属注入太快太猛,搅起空气,形成湍流。
熔炼过程中水分变成氢气,跑不掉就被困住了。
使用太多或劣质的脱模剂,也可能产生挥发气体。
怎么避免?
用干净、干燥的金属锭。
控制注射速度、压力和温度,不要过热。
精准设计流道和浇口,保持流动顺畅。
高品质、用量受控的脱模剂是关键。
2. 收缩孔隙:冷却时的“缩水烦恼”
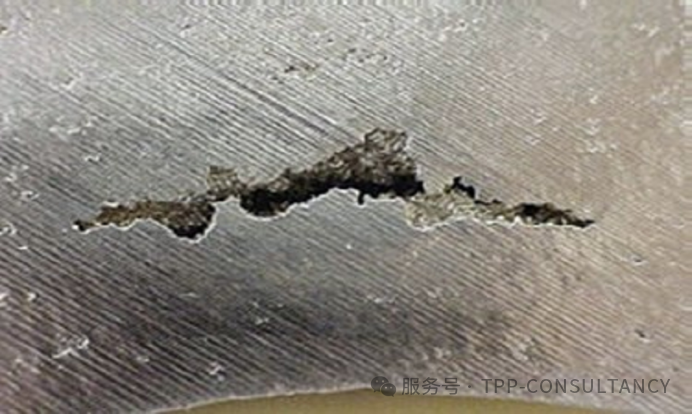
金属冷却时自然会收缩,如果收缩不均,就像地基不稳的房子——不是扭了形,就是塌了角,留下的就是“缩孔缺陷”。
这种缺陷不像气孔那样光滑,而是边缘锯齿状,看起来像裂开的小洞。常见的表现包括:
开放缩孔:铸件表面出现凹坑或管状空洞。
封闭缩孔:藏在内部,看起来像锯齿或尖角。
翘曲变形:凝固过程不均,导致铸件某些部位弯曲、翘起。
为啥会这样?
某些区域金属过多,冷得慢。
注射压力不够,金属流动不足。
浇口和流道设计不当,导致填充不均。
模具或熔融金属温度控制不佳。
怎么解决?
简化铸件几何结构,让金属更好流动。
用铸造模拟软件优化设计。
增加压力,让金属填满每个角落。
安装冷却器或散热片,帮助金属均匀冷却。
3.水槽现象:金属表面的“小坑洼”
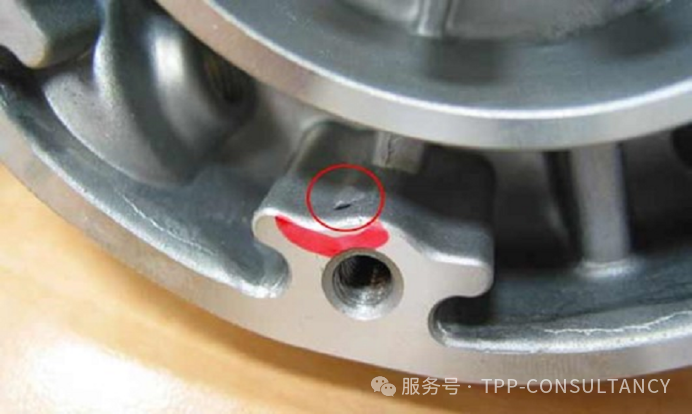
你有没有见过一件金属件表面凹进去了一块,好像被什么东西按了一下?这并不是模具的问题,而是铸件在冷却时“自己塌了下去”——这就是水槽缺陷,也叫下沉现象。
想象一下,当铸件某个部位金属特别厚,冷却得比较慢,内部又没有足够的金属补进去填满空间,表面自然就会凹下去,就像煮熟的馒头塌了顶。这种凹陷通常出现在金属比较厚的区域,表面光滑、还能反光,肉眼就能看出来。
它是怎么发生的?
铸件的壁厚不均匀,就像有的地方是“厚外套”,有的地方是“短袖”,冷却收缩不一致。
模具某个区域温度太高,导致金属在那儿冷得特别慢。
模具内部空气出不去,气体“憋”在液态金属和模壁之间。
金属注射压力太低,补料不够。
金属填充后保压时间太短,还没来得及把空隙填满就结束了。
怎么避免?
4.夹渣:藏在金属里的“小脏东西”
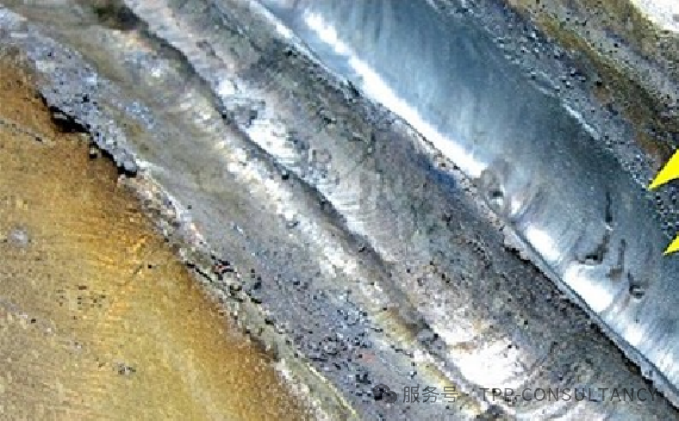
想象一下,一块刚做好的金属件表面看着不错,可仔细一看,却有些粗糙不平,甚至带着点斑斑点点的“结壳”感。这种情况,很可能是被夹渣污染了。
夹渣,顾名思义,就是炉渣、沙粒、氧化物等非金属杂质混进了金属里。这些杂质一旦进入铸件,不仅影响外观,更严重的是会削弱材料的强度和性能,就像食物里混进了沙子,吃着硌牙还不健康。
夹渣的外观通常呈现出不规则形状,像一条条带子或鼓起的小包,有棱有角,表面看起来就不太对劲。虽然它们可能只有几毫米厚,但大多数情况下肉眼就能发现。
这些杂质是怎么跑进来的?
熔融金属在浇注过程中,带上了还没清理干净的炉渣颗粒。
浇注系统设计不合理,让杂质趁虚而入。
金属冷却过程中生成了不溶的金属化合物,结果它们浮不起来,反而被困在了铸件里。
往金属液里加入的合金材料没有完全融化,也变成了“夹杂物”。
怎么避免这种问题?
5.浮渣:浮在金属上的“泡沫垃圾”
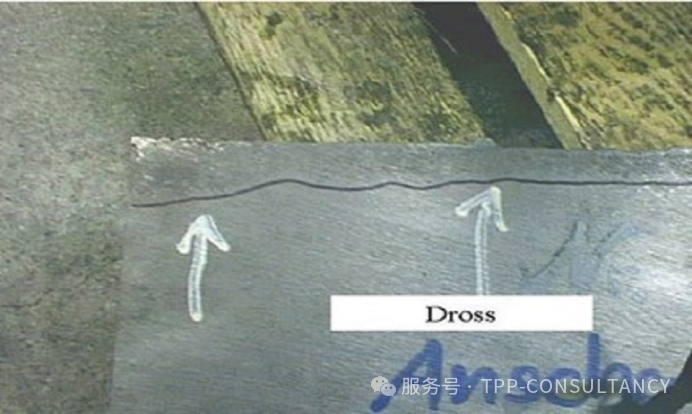
在金属铸造过程中,有一种不太起眼却常见的问题,叫作浮渣。它就像金属熔化后漂在表面的一层“泡沫垃圾”——看着不起眼,却会实实在在地影响铸件质量。
当金属熔化时,会和空气中的氧气发生反应,形成一层氧化物杂质,这层杂质漂浮在金属液体表面,我们就把它叫做“浮渣”。如果在浇注过程中没能清理干净,或者金属液体搅动过猛,把这些浮渣带进了模具,那就可能在铸件中留下“污染物”。
特别是在铝合金铸造中,浮渣更是个“老大难”。高温下,铝容易发生所谓的“铝热反应”,加速氧化,浮渣就越多。
它是怎么形成的?
如何避免让浮渣“下锅”?
尽量避免搅拌熔融金属,尤其是在即将浇注的时候。
降低金属的加热温度,别让它“发火”太猛。
缩短熔炼时间,别让金属在高温下“泡太久”。
6.焊接缺陷:铸件“粘”错了地方

你有没有见过一件压铸件,边缘看起来有点“粘连”不清,或者某些地方多了一块奇怪的金属?这很可能是发生了焊接缺陷——但别误会,这里的“焊接”不是焊工在动手,而是熔融金属自己“搭错了边”。
所谓焊接缺陷,其实是金属在模具里没流好。当高温下的液态金属喷入模具时,如果流动不顺畅、压力不均或模具有点小毛病,就容易出现这种情况——金属粘在模腔表面上,等冷却后铸件一取出来,模具那一块的金属也“蹭”出来了。
结果就是:
它是怎么发生的?
模腔本身有磨损或表面太粗,金属容易“挂住”。
注射系统没调好,金属喷得歪了,方向不对。
金属温度或模具温度太高,金属流得太快、太粘。
脱模剂质量差,或者喷太少(或太多)了。
合金配比不合理,特别是铁含量太低。
怎么解决这“自作主张”的焊接?
热相关缺陷
金属虽然天生耐高温,但在铸造过程中,温度太高或太低都可能带来麻烦。所谓热相关缺陷,就是金属在受热或冷却过程中“发脾气”了,出现了各种不该有的问题。主要有三种:热泪、冷隔和中暑。听起来像人在热天的反应吧?咱们一一来看。
1. 热泪:金属的“情绪裂纹”
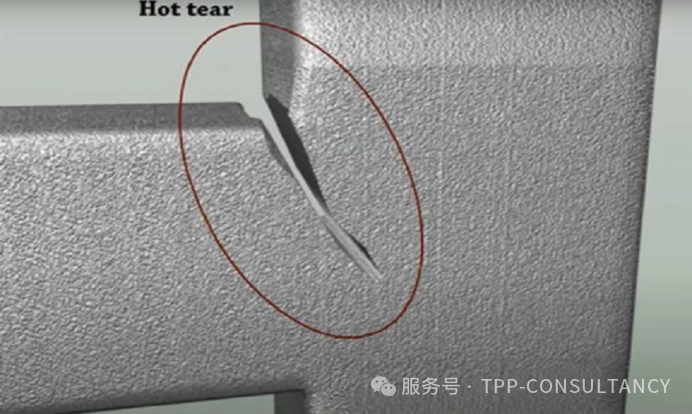
“热泪”这个名字听起来挺诗意,其实是铸造中很常见的一种高温撕裂现象。它发生在金属开始凝固但还没完全硬化的时候,这个阶段金属表面很脆弱,一旦受力,就可能撕开一道裂缝。
这些裂缝通常呈线状或不规则形状,出现在接头、拐角等“承压点”,看起来就像金属在“流泪”。
为什么会出现?
金属冷却收缩,但没有足够空间释放压力。
浇注温度不够,金属凝固太快。
浇口设计不合理,导致凝固顺序错乱。
怎么避免?
在接头等区域使用圆滑过渡设计,减少应力集中。
优化浇口位置,让金属凝固得更自然。
采用标准的冷却和凝固方案。
保持材料厚度一致,避免局部应力积聚。
2. 冷隔:金属“没握好手”
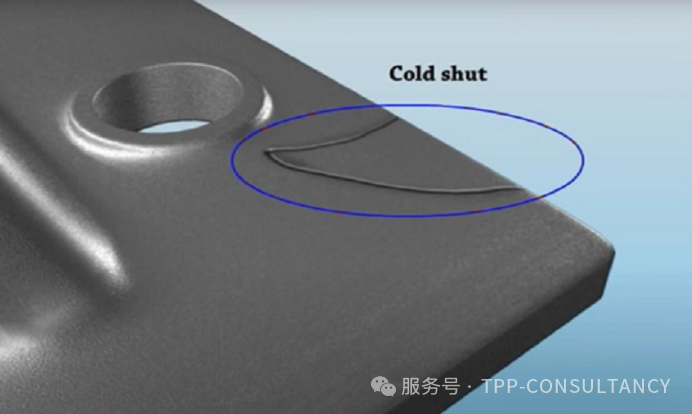
冷隔就像是金属“握手失败”的结果。它发生在多个金属流从不同方向同时进入模具,却因为温度太低,没能很好地融合,留下了一道圆边裂缝,看起来像“裂了一半”。
这就像做蛋糕时面糊搅得不够,烤出来中间有条缝——不美观也不牢固。
造成原因:
浇注系统设计不好,金属“你走你的、我走我的”。
金属液温度太低,流动性差。
铸件某些区域太薄,金属流过去就冷了。
解决办法:
优化流道设计,让金属合流时更加顺畅。
提高浇注温度,别让金属太早冷掉。
提升模具透气性,防止气体阻挡金属流动。
3. 中暑:模具“热晕了”
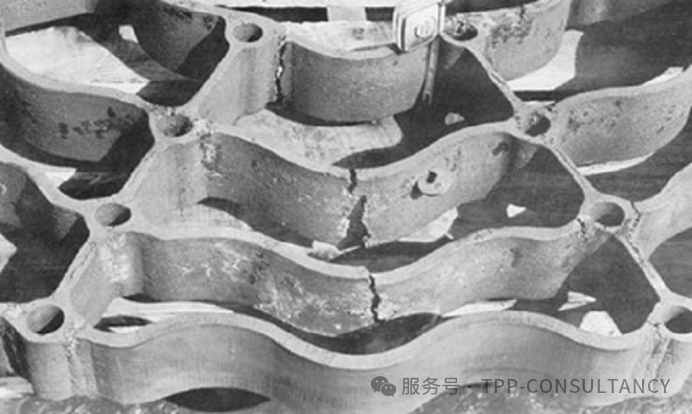
没错,模具也会“中暑”!尤其是铝合金压铸过程中,模具要反复经受高温金属的冲击和冷却循环,时间久了表面结构会疲劳、产生细微裂纹,严重时整块模具都会“撑不住”。
这种“中暑”现象常见于模具边角、靠近浇口的位置,表现为裂纹、脱皮、甚至变形。
原因包括:
模具长期暴露在高温下,热应力不断累积。
模具边缘和角部太尖锐,容易应力集中。
浇口位置太靠近高温区,热量集中释放。
预防方法:
模具材料缺陷
别以为问题都出在金属身上,模具本身如果选材不当、设计不佳或维护不到位,也可能引发一连串麻烦。这些问题通常被称为模具材料的铸造缺陷,它们的表现各不相同,有的像起泡,有的像裂缝,还有的干脆让金属“泄了出来”。
下面,我们来看看这类缺陷中的七种“常见犯规”:
1. 切开与冲蚀:金属太猛,模具扛不住
当高温金属以极高速度冲进模具时,如果模具内的砂子强度不够,就会被冲走,形成多余的金属凸起。这些凸起通常出现在金属流速快的一侧,表面凸起但不是设计的一部分。
为什么会这样?
模具内部某些区域设计不合理,金属堆积太多。
金属流速过高,把砂冲走了。
怎么避免?
优化流道和浇口设计,避免“猛灌”。
增强模具和芯砂的强度。
在芯砂中加更多粘合剂,让它“更能抗”。
2. 融合:模具沙子被烧化了
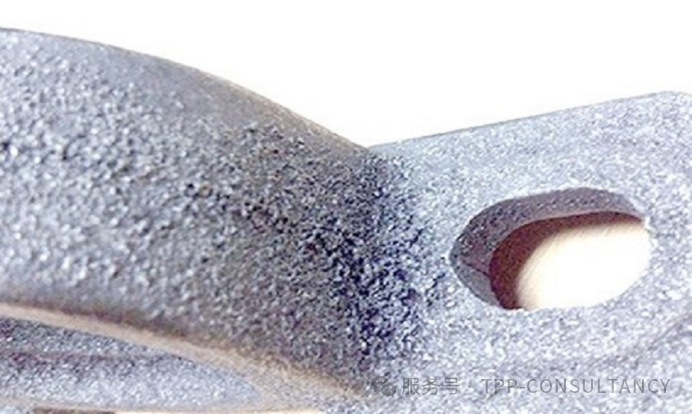
这是砂型铸造中一个“烧杯子”的问题。熔融金属温度太高,砂子的耐火性又不够,结果砂子直接和金属融合,变成一层薄薄的硬壳粘在铸件上,很难清理。
为什么会发生?
砂子的耐火性太差,扛不住高温。
金属温度过高,冲得太猛。
解决办法:
换成更耐高温的模具材料。
降低金属的浇注温度,别烧过头。
3. 漏铸:铸件“缺了一块”
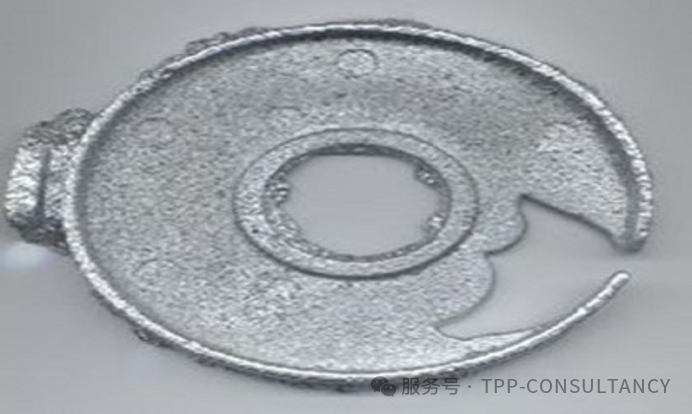
这其实就是金属漏了。当模具或压铸设备出现问题,金属没能填满模腔,就会造成铸件部分缺失,看上去不完整,有时候表面还比较光滑,看着像“漏做了”。
主要原因:
怎么预防?
每次铸造前都检查模具状况。
模具使用耐高温材料,更结实、更可靠。
出问题的模具及时修理或更换。
4. 膨胀:金属“鼓出来”了
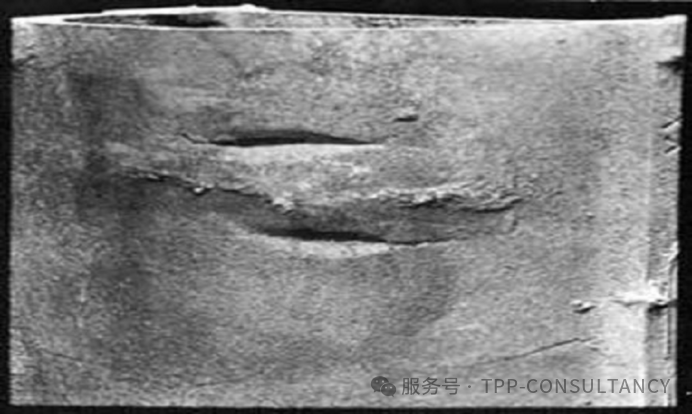
这是一种常见的尺寸问题,模具强度不够时,在金属压力下模壁会“退后一步”,导致铸件表面鼓起或变形,看起来像轻微的“波浪纹”。
可能的原因:
模具材料太软,挡不住金属的静压力。
浇注方式不当,压力分布不均。
解决方法:
用更结实、压得住金属的模具。
模具设计时就考虑受力,别让它“退缩”。
5. 滴剂:模具“掉沙子”了
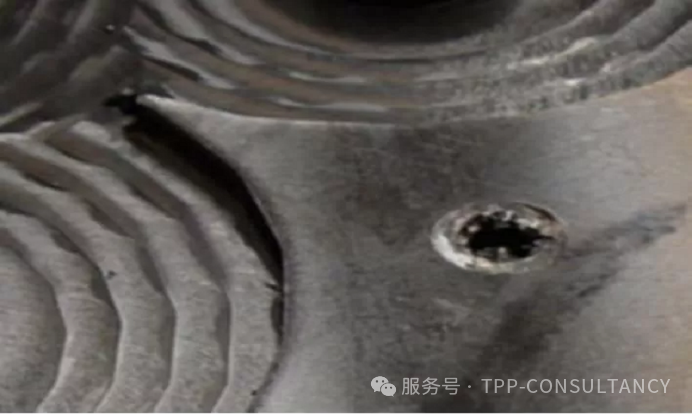
这种缺陷就像天花板掉灰:模具上方松动的沙子掉进了还没凝固的金属里,结果铸件表面就多了个异形的小包块,不仅不好看,有时还会影响功能。
出现的原因:
型砂强度不够,打击不实。
模具突出部分没加固。
熔剂使用不足,杂质清不干净。
怎么解决?
使用更高强度的砂子。
加强上部模具的结构,必要时用钉子或塞子固定。
适量使用助熔剂,清除金属中的杂质。
6. 金属穿透:金属“钻进模具缝里了”
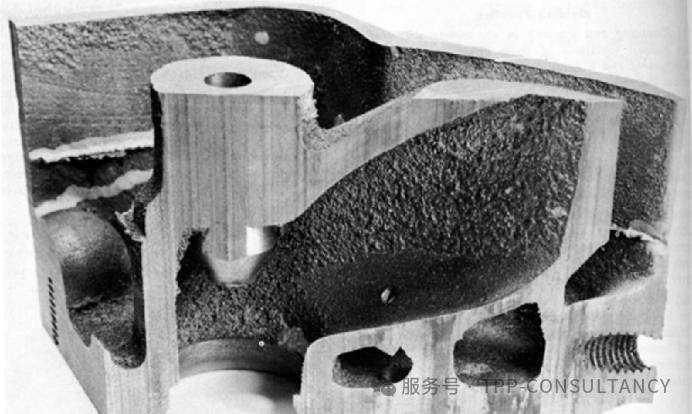
有时候金属会“调皮”地钻进砂子的缝隙中,这就会造成铸件表面粗糙、杂乱,影响美观和尺寸精度。
为什么会发生?
模具砂子太粗,颗粒大、缝隙多。
模具压得不紧,密实度不够。
没有清洁模具,留下了旧渣滓。
怎么处理?
用更细、更强的磨料砂子。
确保模具夯实密实,缝隙小。
使用模具清洁剂,保持模具表面干净。
7. 裂纹:铸件上的“怪裂纹”
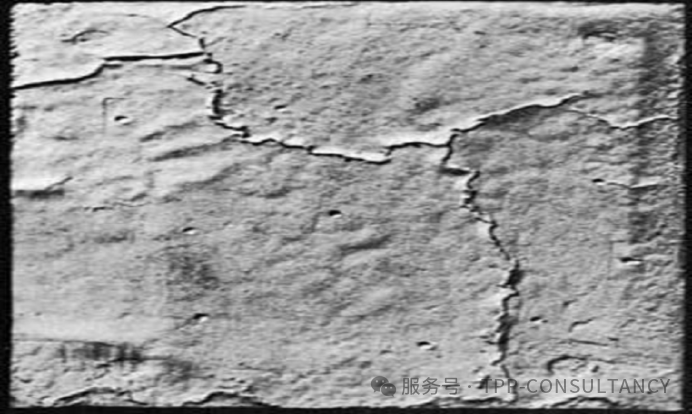
是一种不受欢迎的瑕疵。它表现为细长、不规则的裂痕,像一条尾巴延伸在金属表面。这通常是因为模具在高温作用下,内部膨胀、失稳,导致结构坍塌。
造成的原因:
型砂的抗热膨胀性太差。
模具设计不合理,结构太脆弱。
金属注入温度太高。
预防方法:
在型砂中加入特殊添加剂,提高耐热性能。
降低浇注温度。
优化模具结构设计,适当“让它弹性一点”。
铸件形状缺陷
在铸造过程中,有时候铸件的整体结构没问题,材料也挺好,但外形却总觉得哪里“不对劲”——不是偏了、歪了,就是边上多出一层“毛边”。这类问题就属于铸件的形状缺陷。
这种缺陷主要分为两种:不匹配 和 飞边。前者是模具没装好,后者是金属“偷偷溜出来”了。我们一起来看看它们各自的“罪状”。
1. 不匹配:模具装歪了,铸件也歪了
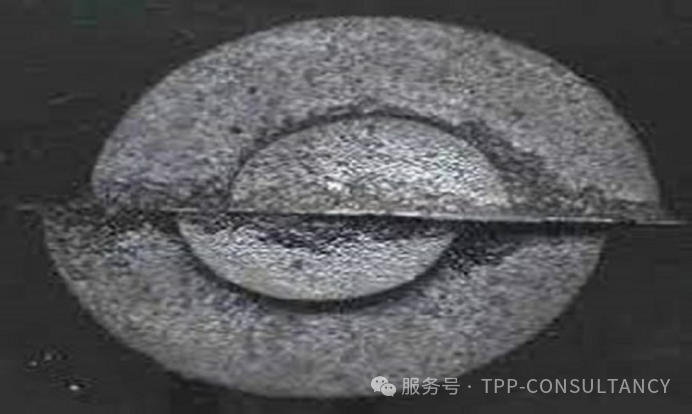
不匹配,顾名思义,就是模具的上下部分对不齐。想象一下拼图没拼好,缝隙错开了,结果就是铸件表面出现台阶或错位,看上去不整齐,摸起来也不顺手。
不匹配又分两类:
模具偏移:上模和下模没有水平对齐,导致铸件左右错位。
型芯偏移:内芯没有垂直对位,会让孔位或内腔出现上下偏差。
为什么会错位?
模具定位销松动,模具在合模时“滑了一下”。
模具设计图案不精确或磨损变形。
模具没放稳,导致装配时角度偏差。
怎么预防?
确保定位板和销钉安装精准,模具闭合牢靠。
使用合适的模具框和加固装置,提升稳定性。
定期检查模具结构,及时维修或更换。
2. 飞边:金属“偷偷溜出去”的小尾巴
飞边是一种压铸中常见的“小烦恼”,指的是在铸件分型线上出现的多余、薄薄一层金属片。就像蒸包子时,面团从盖子缝隙里鼓出来一点点,虽然不影响整体结构,但既不美观,也容易在后期加工时出问题。
飞边的形成原因通常有:
模具闭合不严,夹紧力不够,金属从缝里溜了出去。
分型面有杂质或残渣,造成合模不紧。
注射压力或金属温度太高,金属冲得太猛。
模具材料疲劳,合模面磨损或变形。
如何避免飞边?
形状缺陷虽然不像内部气孔那样“隐蔽”,但它们对产品的外观和装配精度同样影响巨大。想要铸出“长得标准”的好产品,模具对准、压机给力、参数精准缺一不可。
如果需要了解更多内容,欢迎与我们联系,我们将提供专业的管理咨询和数字化解决方案帮助我们的顾客。
邮箱:Marketing@tppconsultancy.com
电话:400 102 1300
微信公众号
