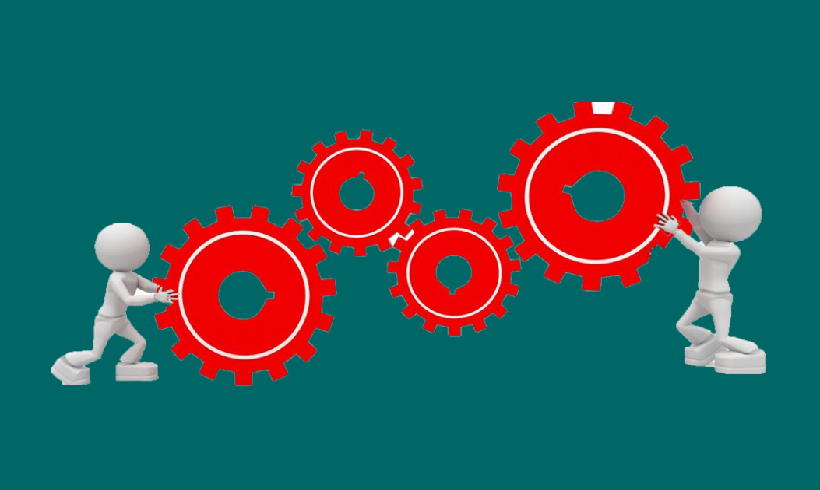
APQP策划好比是盖房子我们从地基开始一层一层地按照标准定义的方法去完成最后这座房子就非常坚固结实了。本文整理了关于APQP实施的8个步骤也是很多主机厂普遍做法希望能给您带来帮助。更多APQP的内容请关注我们9月21-22日APQP的公开课。1.质量管理体系认证:供应商必须拥有IATF16949或ISO9001资质认证。在汽车行业中,IATF16949通常是基本要求。
2.风险评估:除了基本认证外,我们使用特定的评估工具来分析供应商的多个方面:
技术和工艺能力
财务状况的风险水平
生产体系管理的安全性
质量管理体系的可靠性
合格供应商清单(QSL):
供应商必须满足上述两个基础条件后,才能被纳入我们的合格供应商清单(QSL)。
后续步骤:
保密协议和战略合作备忘录:进入QSL的供应商需要与我们签订保密协议和战略合作备忘录,以确保双方在项目开展过程中的信息安全和长期合作。
新项目竞标:一旦合作文档签署完成,供应商将会收到新项目的竞标邀请函。
通过这个流程,我们不仅保证了供应商具备与我们合作的基础能力,还确保了一个系统性和一致性的方法来管理和评估供应商,这在APQP实施过程中是至关重要的。这样做有助于降低风险,提高产品质量,从而达到更高的客户满意度。
第二阶段:供应商定点与报价策略
供应商参与新项目报价
一旦供应商成功入选合格供应商清单(Qualified Supplier List, QSL),便有资格参与新项目的报价竞标。
客户的资料准备
客户会为供应商提供以下关键资料以便于精确报价:
产品图纸
特殊特性清单
项目时间节点
质量和可靠性目标
物流与包装要求
禁用物质清单
客户的特殊要求
供应商质量工程师(SQE)的角色
全面评估供应商报价:SQE需要确认供应商是否全面考虑了所有客户提供的资料和要求,在报价过程中实施综合评估。
警觉不专业的报价行为:任何报价过程中表现出马虎或缺乏全面考虑的供应商都需要被标记。这通常暗示着在前期供应商筛选阶段可能存在遗漏,特别是在“产品报价流程管理”方面。
价格与质量权衡:SQE应该不仅仅关注报价,而是需要综合考量质量、可靠性和成本等多个因素。这符合APQP的核心原则,即全面质量管理。
部门协作与制衡:以一个示例为例,若有三家供应商A、B、C分别报价100、105和65,采购部门可能会对最低报价的C产生兴趣。然而,SQE需谨慎处理这种情况:
质量警示:SQE需要与采购部门紧密沟通,确保他们理解低价格可能代表潜在的质量风险或不符合项目要求。
项目全面性:APQP的目的并不仅仅是部门之间的制衡,而是全面质量管理和跨部门协作。因此,SQE需要确保所有部门,在这里特别是采购部门,充分理解并遵循这一原则。
综合以上各点,SQE在供应商定点与报价策略阶段的角色不容忽视,特别是在贯彻APQP要求方面。这不仅有助于确保项目的质量和可靠性,还促进了部门间的有效协作。
供应商最终确认
经过初步筛选和竞价报价阶段,最终的供应商将被确定。根据项目的规模和预期需求量,可能选择一家供应商或采用多家供应商的策略。
官方任命与合同条款
选定供应商后,客户通常会发出正式的任命书,其中包括以下重要信息:
技术文件的最终版本
质量目标定义
物流协议
产品生命周期预测
模具和工装费用
产品质保期限
索赔要求
年度成本降低计划
设计评审与质量保证
设计评审:在项目启动阶段,客户和供应商需要进行一轮设计评审,确保对图纸中的特性和尺寸有共同的理解和确认。
质量确认与协商:供应商需要提供相应的质量保证方案。如果存在分歧或特定特性无法保证,此阶段仍有协商余地。双方可通过签署偏差协议或更新图纸来达成一致。
整改方案:如果某些特性无法调整,供应商必须提供整改方案,如购买新设备或添加新工序,以确保满足质量要求。
材料替代考虑
特别是对于某些外资企业,材料代用是在这个阶段需要考虑的重要因素。例如,供应商可能希望在不影响性能的前提下,将原材料替换为成本更低、更易获取的国内材料。
供应商质量工程师(SQE)的角色
质量确认与验收:SQE需要确保供应商提供的质量保证方案或整改方案符合客户的质量和可靠性要求。
跨部门协调:SQE与研发部门需要紧密协作,对供应商的质量保证能力进行综合评估。
风险评估:SQE需要针对任何可能的质量或供应风险进行评估,以便提前进行规避或制定应对措施。
综合上述要点,供应商质量工程师在供应商确认与项目启动阶段起着关键作用,尤其是在实施先进产品质量规划(APQP)要求方面。有效的供应商管理不仅有助于确保项目质量,还能促进多部门之间的有效协作和资源优化。
初始样品与模具
到达这一阶段时,供应商应已完成软模或硬模的制造。软模通常用于初步测试,而硬模则表明供应商对产品的高度信心。在这一点上,原型样品(在没有设计能力的国内供应商场景中通常称为Off-Tooling Sample, OTS)应该已经制造完成。
样品测试与性能验证
尺寸特性测试:拿到OTS样品后,立即进行产品尺寸特性的测试。
性能测试:同时,开始进行产品的性能测试。
如果产品是供应商自行设计的,这些原型样品通常被称为初始样品。在这种情况下,需要针对原型样品进行匹配性确认,然后再指导供应商进行设计更新。
质量管理文档
在这一阶段,供应商应基于其经验和能力完成以下质量管理文档:
初始版本的失效模式与影响分析(FMEA)
过程流程图(Flow-chart)
控制计划(Control Plan)
产品追溯方案
设计建议与变更
如果在这一过程中有针对性的设计建议,即这些建议能简化供应商的制造过程同时不影响产品的功能和性能,应及时与客户沟通并提出设计变更。
供应商质量工程师(SQE)的角色
样品与设计确认:SQE需确保供应商正确地理解和执行了所有设计和质量要求。
质量文档审核:SQE负责审核供应商提交的FMEA、过程流程图、控制计划和产品追溯方案,确保它们符合先进产品质量规划(APQP)的标准。
变更管理与沟通:SQE在任何潜在的设计变更中起到桥梁作用,负责与客户和供应商之间进行有效的沟通。
通过这一阶段的严格管理和质量控制,SQE不仅确保了产品质量和生产流程的稳健性,还有助于实现多部门之间的有效协作和资源优化。这符合APQP的核心宗旨,即通过全面和结构化的方法来确保产品质量和可靠性。
OTS样件认可与模具冻结
一旦客户认可了供应商提交的Off-Tooling Sample (OTS) 报告,这标志着供应商可以进入生产过程开发阶段。
此时,模具可以被冻结,不再需要进一步的修改。需要明确的是,客户认可的OTS报告并不意味着所有尺寸必须严格符合图纸标准,但必须确保偏差不影响产品的使用和功能。
内部文件更新与员工培训
全尺寸报告:供应商需提交OTS全尺寸报告,并获得客户的认可。
质量管理文档更新:在内部更新PFMEA(过程失效模式与影响分析)、Control Plan(控制计划)和Flow Chart(过程流程图)。
岗位作业指导书与员工培训:编制岗位作业指导书,并根据其内容对生产线工人进行培训。
测试方案与人员培训:冻结产品的测试方案,并对测试人员进行相应的培训。
量具与检具的R&R(重复性与再现性):确保所有测量和检查工具的可靠性和准确性。
下一级供应商认可:进行下一级供应商的质量评估和认可。
模具维护计划:根据模具状态,制定相应的模具维护和保养计划。
过程性能验证(PPK):进行生产过程的PPK验证以确认过程稳定性。
SQE角色与客户审核
内部试生产与确认:在所有文档和过程都准备就绪之后,供应商应进行内部试生产。一旦确认没有问题,便可邀请SQE进行过程审核(Process Audit)和产能核算(Run@Rate)。
客户验证与PPAP提交:若SQE的过程审核和产能核算均无问题,供应商应将PPAP样件、全尺寸报告和PPAP文件包提交给客户以进行最后的验证。
通过这一阶段的严格质量控制和多层次的验证,SQE有助于确保生产过程的稳定性和产品质量,进一步实现Advanced Product Quality Planning (APQP)的要求。这不仅强化了供应商和客户之间的信任关系,还有助于缩短产品上市的时间并提高市场竞争力。
等待PSW(Part Submission Warrant)认可
在本阶段,主要任务集中在客户端,供应商的主要责任是等待客户对Part Submission Warrant(PSW)进行签署。PSW的签署是一个具有挑战性的步骤,不同客户可能有不同的签署程序和责任人,例如,某些客户要求由负责的供应商质量工程师(SQE)签署,而其他客户则要求由质量经理签署。
客户试跑、试装与功能性验证
客户将进行一系列验证工作,包括但不限于产品试跑、试装和总成的功能性验证。这些步骤对于PSW的最终认可至关重要。
进入生产启动(SOP)
一旦所有验证步骤成功完成,客户通常会签署PSW,正式宣布产品进入生产启动阶段(SOP)。然而,需要注意的是,出于各种原因,包括但不限于质量控制和风险管理,客户有时会延迟PSW的签署。
供应商应持续关注与沟通
虽然这一阶段主要由客户负责,供应商仍需保持高度关注,并与客户保持密切沟通,以便及时了解PSW认可的进度和可能的问题。
通过遵循这一流程,SQE不仅有助于确保供应商能够满足Advanced Product Quality Planning(APQP)的要求,而且还有助于建立和维护供应商与客户之间的长期合作关系。同时,这种专业的管理方式也有助于缩短产品上市周期和提高产品质量,进一步增强企业的市场竞争力。
实施一级受控发运(CSL1)或GP12
在客户宣布产品进入量产阶段后,通常要求供应商执行至少三个月的一级受控发运(Controlled Shipping Level 1,简称CSL1)或也称作GP12。这意味着供应商必须在生产线末端进行全面质量检验,并据此发货给客户。
持续质量汇报
在这三个月的受控发运期间,供应商需持续向客户报告全检结果。这些报告应详细、准确,并按照预定的频率和格式进行,以便客户能准确评估产品质量和流程稳定性。
质量稳定后取消一级受控发运
如果在这三个月内,全检结果显示产品质量稳定且符合客户设定的质量标准,客户通常会宣布取消一级受控发运,进而转入常规的质量管理和发货流程。
供应商质量工程师(SQE)的角色
作为SQE,您应确保供应商准确、有效地执行以上步骤,并与客户保持良好的沟通。此外,您还需密切关注全检结果,以便在出现质量波动时能迅速采取纠正措施。
遵循这一流程,SQE不仅确保供应商符合Advanced Product Quality Planning(APQP)的要求,而且也建立了一套有效的次品遏制机制,进一步提升了供应链的整体质量和效率。
确保供应链的稳定性:遵循QCD指标
进入量产阶段后,供应商的主要任务是根据客户订单,按质按量按时进行发货。在这一环节,供应商应严格遵循质量、成本和交货时间(QCD)的核心指标,以确保供应链的稳定性和高效性。
持续改进与成本优化
同时,供应商应积极进行持续改进活动。这是因为持续改进不仅是提升产品质量和流程效率的关键,也是实现年度成本降低目标的有效手段。这些活动可以包括,但不限于,流程优化、物料替换和生产效率提升等。
供应商质量工程师(SQE)的职责
作为SQE,在这一阶段您应负责监督供应商执行上述任务,并确保其符合Advanced Product Quality Planning(APQP)的标准和要求。您还应与供应商合作,识别和实施持续改进活动,以满足或超越客户的质量和成本目标。
总结
遵循APQP的开发步骤不仅有助于项目顺利进入量产,而且通过持续改进,也有助于长期维护和提升供应链的整体性能和竞争力。因此,SQE应确保供应商在APQP框架下,能持续地实现产品和流程的优化。