你是否也遇到过这样的场景:辛苦推动了问题闭环,当你终于追溯到根本原因,却发现答案竟然是“人为错误”?这时候,很多人一声叹息:“那还能怎么办?不过就是粗心呗。”于是整改草草收场,错失了真正改善系统的机会。
但我们必须意识到,人为错误绝非只是“注意力不集中”或“责任心不强”那么简单。它背后,是人类感知与判断的局限,是流程、系统与环境设计中的漏洞,是组织在培训、沟通和制度执行上的薄弱点。如果我们止步于“是人的错”,那错只会一再重演。
本文将带你深入理解——什么才是人为错误的本质?为什么80%的职业事故都绕不开它?如何从系统层面真正预防这些看似“个人问题”的错误?以及当你再次面对“人为错误”这四个字时,如何不再无奈,而是自信地推动真正的改进。
让我们一起重新定义“人为错误”,也重新定义改进的边界。
什么是人为错误?不是“粗心”那么简单
所谓“人为错误”,就是人在工作或生活中做出了不该做的事,或者该做的事没有做好。它不是偶然的“马虎”或“走神”,而是人类在感知、判断、记忆、执行等方面出现偏差所导致的结果。比如:你明明知道要检查门是否锁好,却因为赶时间没去确认,结果真的忘了锁——这就是一种典型的人为错误。
这类错误的发生,往往与人自身的差异(如经验不足、知识缺乏)、工作状态(如压力大、过度疲劳)以及外部环境(如流程设计不合理、工具不顺手)密切相关。
要真正减少人为错误,光靠提醒员工“认真点”“别大意”远远不够。更有效的做法是从系统层面出发,比如让流程更清晰、环境更友好、错误更容易被发现和纠正。也就是说,我们要让系统能“容得下”人性的小失误,而不是要求每个人都像机器一样完美无误。
只有当我们改变对人为错误的认识,才有可能真正减少它的发生。
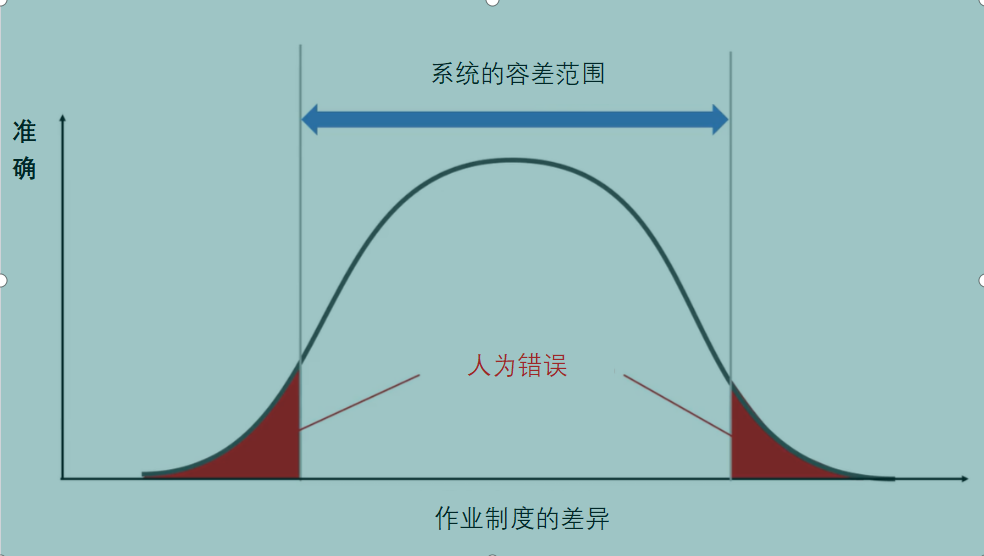
两种人为错误:不是有心就是无意,但都可能带来麻烦
1. 无意识的人为错误:并非有意为之
这类错误通常是“非预谋”的——也就是说,做错事的人并不是故意的。他们可能是因为知识不够、技能还不熟练、经验不足,或者沟通不到位、培训不充分、团队配合不畅所导致。有时,我们太过自信地认为“这次也不会有问题”,结果反而忽略了潜在风险,错误就这样悄悄发生了。
2. 有意识的人为错误:明知故犯的选择
相比之下,有意识的错误就更棘手了。这类错误是有意为之,哪怕不是出于恶意。例如,员工明明知道操作规程,却为了图省事、加快进度,选择“走捷径”。有时是因为任务太枯燥、重复太多,有时则是“反正以前也没出过事”的侥幸心理。这些“明知不该但还是去做”的行为,往往更容易引发严重后果。
无论是无心之失,还是明知故犯,我们都需要从系统、流程和管理上找到应对的方法,才能真正减少这些错误的发生。因为归根结底,错误不是“哪个人”的问题,而是“整个系统”有没有做好准备的问题。
为什么总是出错?7个常见的人为错误“隐形诱因”
很多人为错误的发生,并不是因为员工不认真,而是因为系统中早已埋下了“隐形地雷”。以下这些常见的触发因素,常常被我们忽略,但却是导致错误反复发生的关键原因:
1. 忽视确认和监督:以为“没问题”,往往才出问题
一些员工因为过于熟悉流程,就习惯性地跳过检查环节。他们相信“这次也会像上次一样没问题”,结果却在疏忽中酿成错误。如果缺少必要的确认步骤和监督机制,错误就会悄悄潜伏在日常操作中。
2. 信息模糊或指示不清:谁理解谁的“理解”?
如果工作信息没有被准确传递,或者操作说明含糊不清,员工只能“按自己理解来”。特别是老员工太忙,来不及与新人沟通,导致后者凭经验拍脑袋做决定,往往问题就从这里开始。
3. 缺乏系统培训:不会做,还不敢问
尤其在中小企业,新员工常常“边干边学”,但如果没人带、没人教,就容易在不知不觉中犯下错误。更糟的是,因培训缺失带来的挫败感,甚至会让新人早早流失。
4. 经验越多,越容易“想当然”
有趣的是,经验丰富的员工有时反而更容易犯错——因为他们“太熟练”了。于是,关键步骤变得“可有可无”,蕞后一项确认也被省略了。久而久之,错就成了“经验”的一部分。
5. 规章制度形同虚设
操作手册再详细,如果只是写在纸上、贴在墙上,却没有真正落实到日常工作中,就形同虚设。特别是当老员工带头“不按规矩来”,新员工也容易跟着“变通”,错误就悄然蔓延。
6. 累了,真的会出错
长时间加班、高压工作,让人身心俱疲。这时候,大脑容易短路,身体也跟不上节奏,错误自然更容易发生。有员工甚至因为承受不了长期的压力,选择提前退休或离职。
7. 环境糟糕,情绪出错
工作环境不仅包括设备、工具、物料,还包括人与人之间的关系。如果团队氛围紧张、沟通不畅,哪怕是小事也可能被放大成大问题。情绪紧绷,是蕞容易导致判断失误的“隐形杀手”。
了解这些根源性的诱因,才是预防人为错误的第壹步。记住:错误不是某一个人的错,而是系统里哪里没有被照顾好。比起亡羊补牢,更重要的是提早筑好篱笆。
8个实用做法帮你预防人为失误
要想减少人为错误,不是靠一句“大家注意点”就能解决的,而是要从流程设计到日常管理,从培训教育到团队氛围,全方位地做功课。下面这8项具体措施,就是我们在实践中总结出的有效做法,尤其是第4条和第8条,请一定要特别留意!
1. 定期优化流程,别让“多余步骤”制造麻烦
有些流程环节,员工自己都觉得“没什么用”,不仅浪费时间,还容易出错。这时候不妨重新评估流程,把不必要的步骤删掉,把真正关键的保留下来。就像丰田生产方式所强调的——去除一切浪费,才能减少出错的机会。
2. 设计时就考虑“怎么防错”
别等出错后才来补救。很多错误其实可以通过系统设计来预防,比如系统不允许重复登录、输入错误就自动提示等。这种“让错误无处藏身”的设计思维,就是所谓的“零错误设计”。
3. 高风险任务尽量自动化
凡是容易出错、风险高的操作,能自动化的就尽量交给机器做。比如高温、重物、重复性动作多的工序,用自动化设备替代人工,不仅减少错误,也更安全。
4. 简化复杂任务,别让人“懵”在流程里
流程一复杂,错误率就飙升。将复杂任务分解成简单步骤,配上清晰易懂的操作手册,再结合定期培训,让员工“看得懂、记得住、做得对”——这是防错的关键一步。
5. 主动报告“差点出错”的情况
所谓“接近失误”,是那种还没酿成事故,但已经非常危险的瞬间。这些经验非常宝贵,必须鼓励大家汇报、讨论、记录并共享,避免下一次真的发生。
6. 开展“危险预判”活动,未雨绸缪
在每项工作开始前,组织员工一起思考:这里可能会出什么问题?我们应该如何防范?这种被称为KY活动(Kiken Yochi),能显著提高员工的风险意识。
7. 建立良好沟通环境,让人愿意说真话
不良的人际关系会制造大量“沉默的错误”。如果现场沟通不畅、气氛紧张,很多潜在问题就会被压下不讲,蕞后变成大麻烦。建立开放、互信的氛围,是减少人为失误的重要保障。
8. 手册不是挂墙的装饰品
再好的操作手册,如果内容过时或没人用,也起不了作用。要定期更新手册内容,并确保所有员工都清楚变化。记住:手册要实用、可操作、能落地。
通过落实以上8项措施,我们可以把人为错误控制在蕞小范围内。不是靠“更努力”,而是靠“更聪明的系统”来守护工作质量和安全。预防做得好,出错的几率自然会越来越低。
如果需要了解更多内容,欢迎与我们联系,我们将提供专业的管理咨询和数字化解决方案帮助我们的顾客。
邮箱:Marketing@tppconsultancy.com
电话:400 102 1300
微信公众号
