字数统计:1234字 预计阅读时间:约3分钟
前言
生产中最常见的人为错误是由于各种原因未能遵循操作,跳过步骤、使用错误的工具和错误的零件,这也是为什么防错在当今的生产过程中至关重要的事情。
同时,消费者对高度定制化产品的需求上升是造成这种故障率的驱动力。由于新产品推出的复杂性和频率不断增加,一次合格已成为关键的 KPI。
传统上,制造商通过大规模批量生产来控制人为错误。随着复杂性的增加,基于精益和过程控制 (SPC) 的制造模式的有效性也开始下降。
这些模式通过额外的防错技术得到增强,例如更详细的操作说明和增加传感器的方法,以控制人为错误。
今天的智能工厂专注于使用新的工业 4.0 技术,例如基于软件的生产防错,以提高产品一次合格率。
方法 1:基于操作工技能和产品成熟度的电子化操作说明
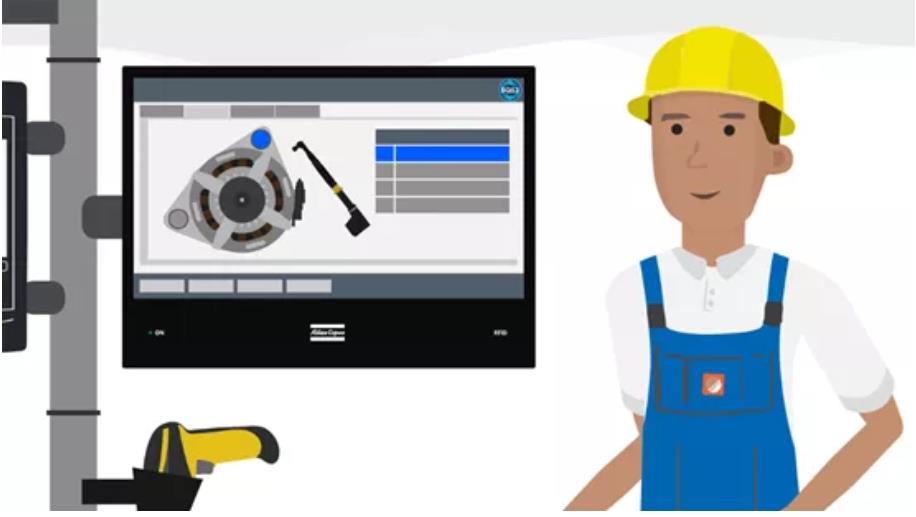
图示——视觉说明引导操作工逐步完成组装过程
交互式装配说明和操作指导与每个工作步骤相关联,并根据操作工的技能水平向他们提供持续的反馈。
例如,管理人员将能够为在线一周的操作工显示详细的步骤进度,而对于 5 年的老手来说,则只显示关键的检查点。与现有的众所周知的流程相比,同样的原则适用于生产线上的新产品或流程。这里的关键词是“交互式”,确保操作工参与并在装配过程的每个关键点进行防错检查。这些检查可防止错误发生或在错误发生后的几秒钟内捕获错误。这种方法大大减少了整体生产停机时间。
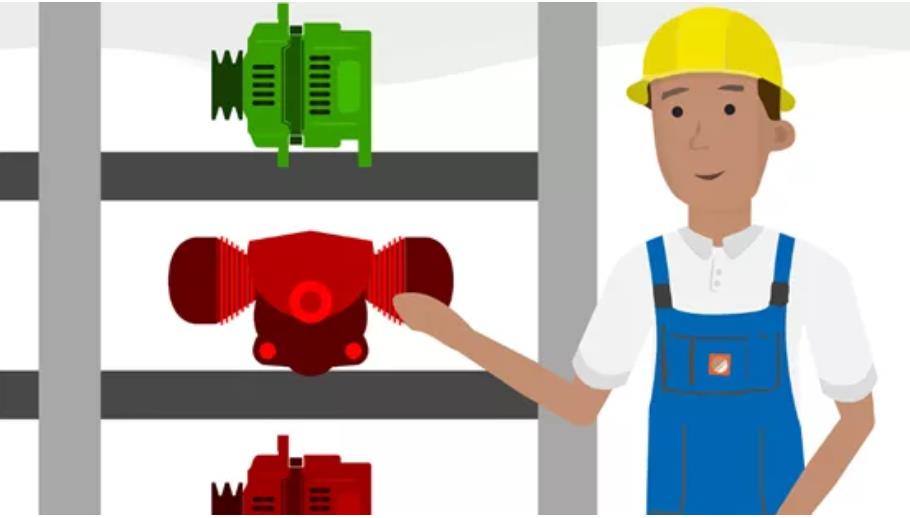
图示——避免操作工组装错误的零件
零件的自动验证使用条形码、RFID 或视觉系统来控制维修和产品召回。越来越多的模型变化和产品复杂性通常会导致人为错误,例如安装错误的相似零件。例如,电子控制模块 (ECU) 外观相似,内部软件不同。通过根据预定义的零件编号自动验证扫描的零件或从材料清单中实时验证来防止组装过程中的错误,可以大量节省返工、维修甚至召回成本。
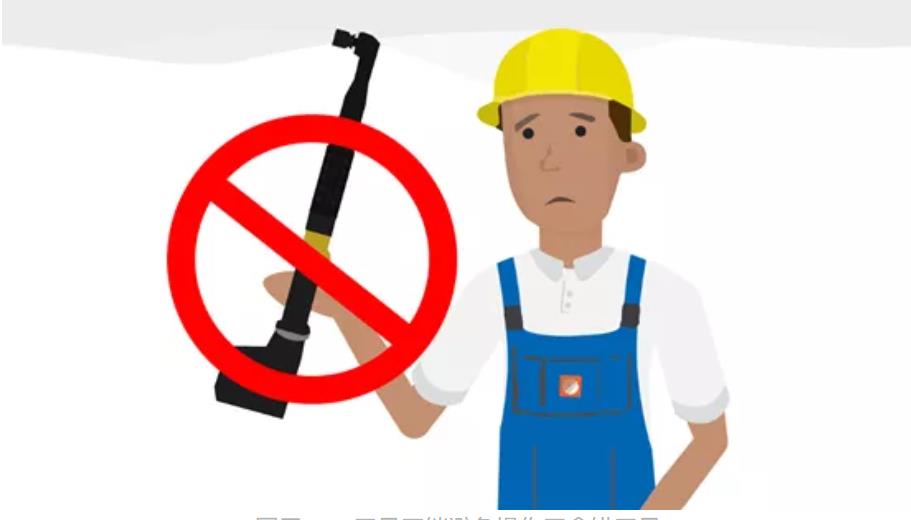
图示——工具互锁避免操作工拿错工具
动态选择工作站中产品变换的正确工具和拧紧规范。使用不正确的工具或规范拧紧螺钉和紧固件的产品极易被召回,从而危及制造商的声誉。通过根据站内产品自动选择工具和程序来进行生产线防错,有助于保护品牌声誉并防止召回责任。
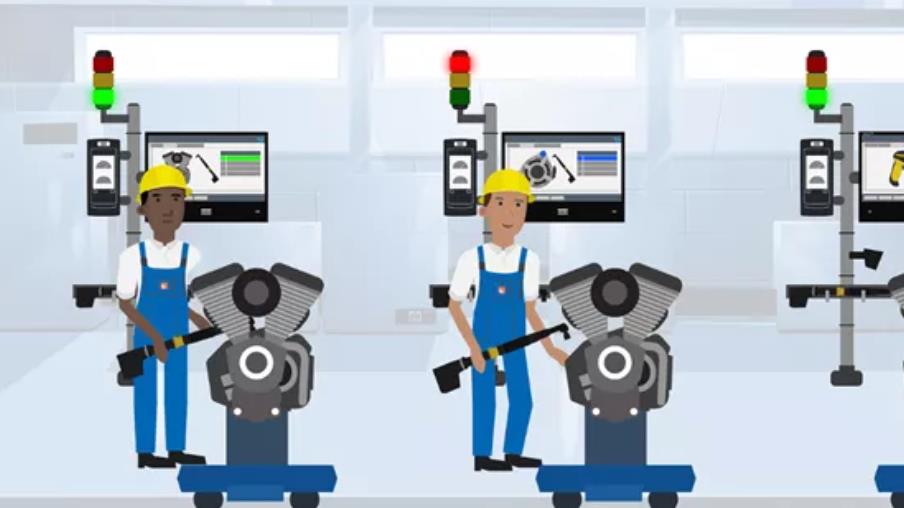
图示——操作工识别以避免未经授权或未经培训的操作工执行任务
控制操作工的访问权限并检查他们的能力认证级别,允许他们执行特定组装任务之前检查他们的能力认证级别是问责制和合规性的必要条件。操作工在日益动态的制造环境中的参与是制造商面临的主要挑战之一。通过提高参与度并最终减少停机时间,确保操作工的责任感是防错的第一步。
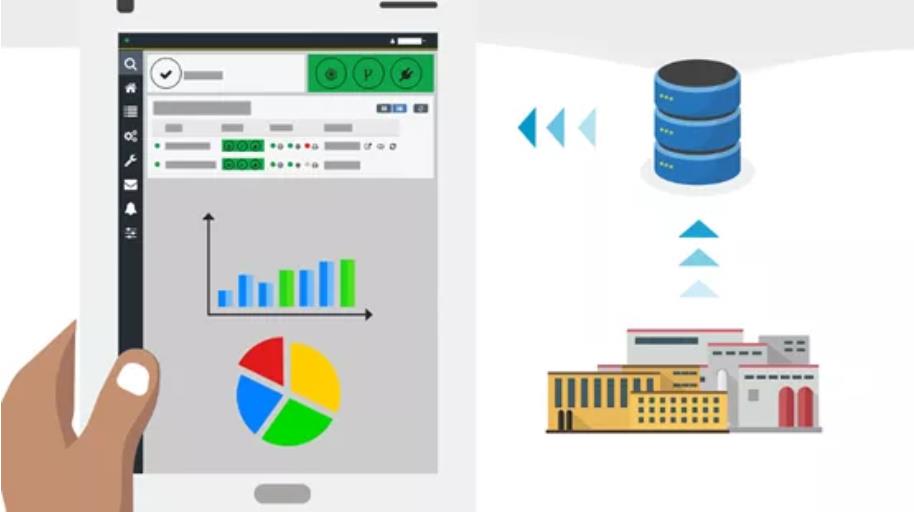
图示——集中的数据收集、存储和过程控制;使用 Web 界面轻松显示
记录数据对于大数据分析、合规性、可追溯性、零件文档和其他用途至关重要。大多数制造商出于法规遵从性目的记录数据,但数据的真正价值在于将其用于防错领域中的优化、趋势分析和预测目的。如果每个客户都收到一份包含他们所购买产品序列号的准确构建数据的出生证明,确认它是按照规格制造的,这对品牌的声誉意味着什么?