例如,虚拟装配是一种数字孪生应用程序,它使用 3D 扫描数据来评估零件如何装配在一起。来自两个或多个零件(例如模具的两侧)的数据被汇集在一起,以虚拟验证它们在现实世界中如何组合在一起。制造商通过使用蓝光 3D 扫描仪的实际数据而不是 CAD 空间中的标称数据来虚拟验证组件的尺寸和精确配合,从而节省时间和金钱,然后再投资于物理组件的生产和分销。
数字装配是支持协作质量控制的类似数字孪生应用程序。通过这种策略,偏远地区的制造商可以共享来自精确 3D 扫描仪的数字孪生数据,以数字方式组装零件并在运送它们进行实际组装之前验证它们的形状、装配和功能。通过验证零部件的准确组装,制造商可以在产生成本之前验证设计并模拟成品。例如,来自航空航天机翼和配合表面结构,或汽车车身和悬挂部件的数据被汇集在一起,以数字方式验证它们在现实世界中如何组合在一起。
使用精确的数字孪生进行仿真还可以帮助克服特定质量控制应用程序常见的挑战,以按预期制造组件。变形称为翘曲,是注塑零件或使用可延展材料的制造商(例如塑料加工商或添加剂制造商)的质量控制的常见问题。质量控制中的翘曲通常是由次优材料或工艺参数引起的不均匀收缩引起的,很难解决。
在某些情况下,识别和量化在无张力状态下发生的整体翘曲有助于工具制造商了解工艺。然而,整体翘曲通常不是功能性问题,有时会随着组装而消失。检查通常与安装或组装状态有关;因此,单个零件中存在的全局翘曲会叠加并歪曲测量结果。
因此,传统上通过测量处于组装或夹紧状态的零件来补偿翘曲。在现实世界中,夹具迫使零件进入过度约束状态,以模拟补偿翘曲所需的组装情况。但是,在可能没有固定装置的早期生产阶段,这不是一个可行的解决方案。
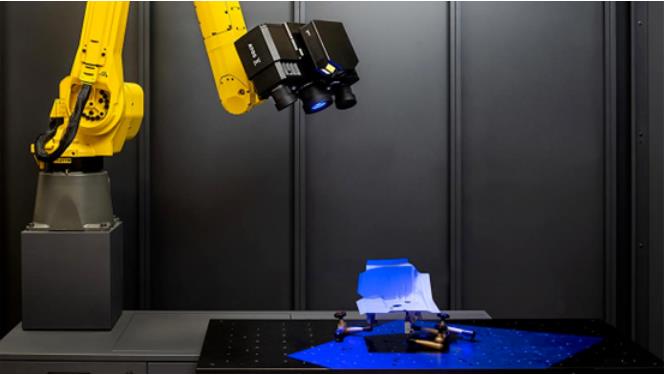
在某些情况下,预算可能不允许投资建设,借助智能 3D 计量软件和蓝光 3D 扫描仪收集的高分辨率数据,制造商可以使用仿真来克服质量控制挑战。
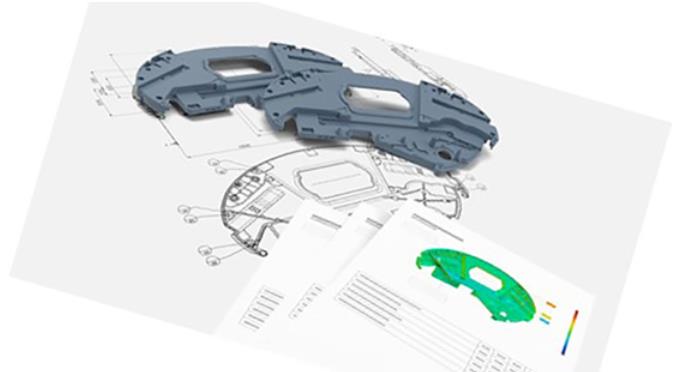
用于计量的数字孪生提供有关物理组件的健康状况、趋势和尺寸的快速而准确的信息,以获得更深入、更有价值的见解。
使用智能 3D 计量软件和准确的蓝光 3D 扫描仪收集的高分辨率数据,制造商可以通过将物理零件的数字孪生置于虚拟夹紧状态来模拟此过程,从而可以像检查零件一样检查尺寸已经处于总装状态。用于翘曲虚拟补偿的算法可以在没有机械夹具的情况下检测过度约束的基准条件。
然后调整数字孪生,并自动重新计算检查结果。制造商可以在夹紧和松开状态之间快速切换,以从评估中检索所需的信息。这种消除翘曲的现代化方法用数字孪生数据和算法驱动的可靠计算取代了物理固定装置,以降低复杂性,在物理世界中执行该过程所花费的成本和典型时间。来自精确 3D 扫描仪的数据还支持可靠的模流模拟,以计算材料特性将如何成型。使用数字孪生数据进行仿真可以预测和预防质量控制问题,从而更快地生产出更好的零件。
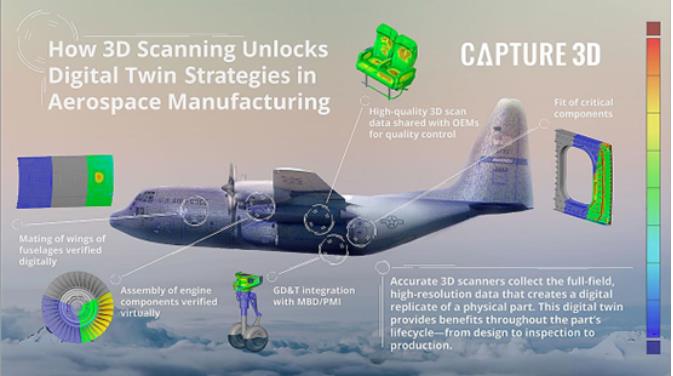
05 Five
历史数字孪生数据以超越其生命周期
历史数字孪生数据为制造商提供了可追溯性,有助于消除重复并通过在零件的整个生命周期中快速比较其状况来优化质量控制。将数字孪生数据编目到每个生产组件的序列号,便于将来检索以进行比较或复制。
除了将零件和组件数字化之外,公司还在扫描他们的最终工具,以计划工具磨损和生产中可能出现的其他不可预见的问题。制造商可以轻松共享数字孪生数据,创建互联的虚拟生态系统,以实现组织内的互操作性、更高的可靠性、增强的性能和敏捷性。通过立即访问准确的数字孪生数据、团队、供应商,
精确的蓝光 3D 扫描仪为数字孪生策略提供了一个途径。他们在每次扫描中收集的数百万个数据点以比手动与物理系统交互更有效的方法生成物理零件、组件或工具的数字化几何标识。用于计量的数字孪生通过仿真改进质量控制和流程。借助有关物理组件的健康状况、趋势和尺寸的快速准确信息,制造商最终可以获得更深入、更有价值的见解。这些见解使制造商能够根据现在和将来的准确数据做出更可靠的决策。